This article has been reviewed according to Science X's editorial process and policies. Editors have highlighted the following attributes while ensuring the content's credibility:
fact-checked
peer-reviewed publication
trusted source
proofread
New study into solute transport and solidification mechanisms in additive manufacturing
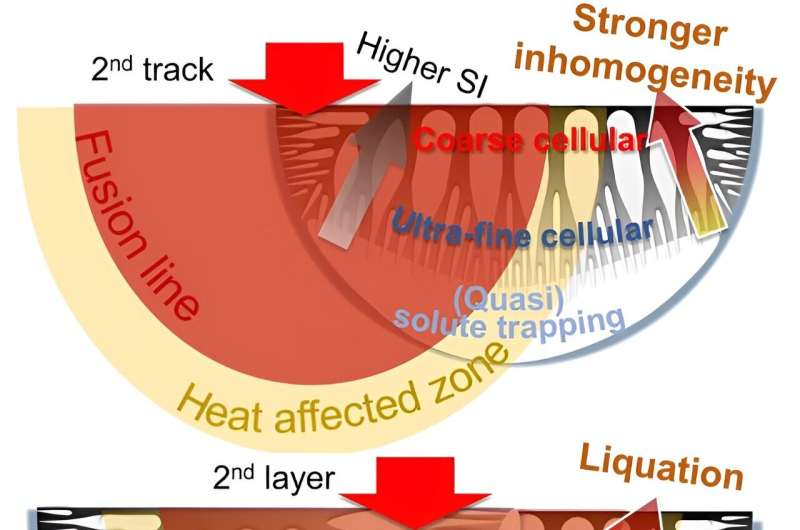
Additive manufacturing (AM), or 3D printing, is a rapidly growing technology with the potential to revolutionize many industries. However, AM parts can be susceptible to defects, such as porosities and cracks, which can limit their performance and reliability.
Researchers at Queen Mary University of London, in collaboration with Shanghai Jiao Tong University, Center of Excellence for Advanced Materials, and University of Leicester, have developed a computational model to reveal how solute trapping occurs during the rapid solidification process in additive manufacturing (AM).
The study, published in Nature Communications, provides new insights into the solute transport and solidification mechanisms in AM, which could lead to the development of new materials and processes for 3D printing.
Solute trapping is a phenomenon that occurs when solute elements are concentrated in certain regions of a solidification front. This can lead to the formation of non-equilibrium microstructures, which can be detrimental to the properties of AM parts.
"Solute trapping is like adding a secret ingredient to a recipe," said Dr. Chinnapat Panwisawas, corresponding author on the study and Senior Lecturer in Materials and Solid Mechanics at Queen Mary University of London. "By understanding how solute trapping works, we can develop new materials and processes that can lead to stronger, more reliable, and more complex 3D printed components."
The researchers used their computational model to investigate the solute transport that occurs during the rapid and repeated thermal cycles in AM. They found that solute trapping is promoted by melt convection, which dilutes the partitioned solute at the solidification front. The researchers also elucidated the mechanisms of the subsequent microstructural transitions to ultra-fine cells and then to coarse cells.
The researchers suggest that their findings could be used to reduce crack susceptibility in AM parts by accelerating the solidification process. They also believe that the detailed solidification pathway they have revealed exhibits promising potential for additively manufactured "hard-to-print" superalloys and aids the future materials design for better 3D printability.
More information: Neng Ren et al, Solute trapping and non-equilibrium microstructure during rapid solidification of additive manufacturing, Nature Communications (2023). DOI: 10.1038/s41467-023-43563-x
Journal information: Nature Communications
Provided by Queen Mary, University of London