This article has been reviewed according to Science X's editorial process and policies. Editors have highlighted the following attributes while ensuring the content's credibility:
fact-checked
peer-reviewed publication
trusted source
proofread
Scientists close the cycle on recycling mixed plastics
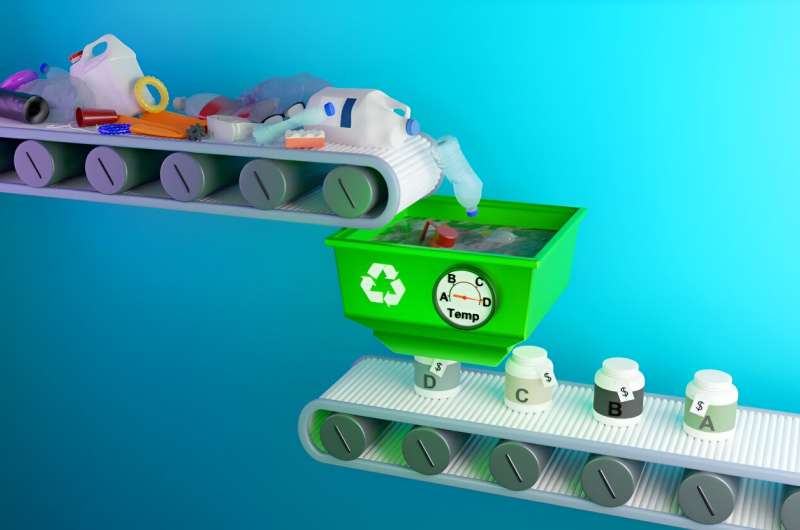
Little of the mixed consumer plastics thrown away or placed in recycle bins actually ends up being recycled. Nearly 90% is buried in landfills or incinerated at commercial facilities that generate greenhouse gases and airborne toxins. Neither outcome is ideal for the environment.
Why aren't more mixed plastics recycled? It's usually easier and less expensive to make new plastic products than reclaim, sort and recycle used ones. Conventional recycling of mixed plastics has previously meant manually or mechanically separating the plastics according to their constituent polymers.
Addressing the issue, scientists at the Department of Energy's Oak Ridge National Laboratory used carefully planned chemical design, neutron scattering and high-performance computing to help develop a new catalytic recycling process. The catalyst selectively and sequentially deconstructs multiple polymers in mixed plastics into pristine monomers—molecules that react with other monomer molecules to form a polymer. The process offers a promising strategy for combating global plastic waste, such as bottles, packaging, foams and carpets.
The researchers' analysis, published in Materials Horizons, compared using the new multipurpose catalyst to using individual catalysts for each type of plastic. The new catalyst would generate up to 95% fewer greenhouse gases, require up to 94% less energy input, and result in up to a 96% reduction in fossil fuel consumption.
"Our approach involves a tailored synthetic organocatalyst—a compound comprised of small organic molecules that facilitate organic chemical transformations. The organocatalyst can convert batches of mixed plastic waste into valuable monomers for reuse in producing commercial-grade plastics and other valuable materials," said Tomonori Saito, an ORNL synthetic polymer chemist and corresponding author. "This exceptionally efficient chemical process can help close the loop for recycling mixed plastics by replacing first-use monomers with recycled monomers.
"Today, nearly all plastics are made from fossil fuels using first-use monomers made by energy-intensive processes. Establishing this kind of closed-loop recycling, if used globally, could reduce annual energy consumption by about 3.5 billion barrels of oil," Saito added.
A recycling solution for over 30% of all plastics
The new organocatalyst has proven to efficiently and quickly deconstruct multiple polymers—in around two hours. Such polymers include those used in materials such as safety goggles (polycarbonates), foams (polyurethanes), water bottles (polyethylene terephthalates) and ropes or fishing nets (polyamides), which together comprise more than 30% of global plastic production. Until now, no single catalyst has been shown to be effective on all four of these polymers.
The process provides many environmental advantages by replacing harsh chemicals for deconstructing polymers, as well as offering good selectivity, thermal stability, nonvolatility and low flammability. Its effectiveness against multiple polymers also makes it useful for deconstructing the increasing amounts of multicomponent plastics, such as composites and multilayer packaging.
Small-angle neutron scattering at ORNL's Spallation Neutron Source was used to help confirm the formation of deconstructed monomers from the waste plastics. The method scatters neutrons at small angles to characterize the structure at different levels of detail, from nanometers to fractions of a micrometer.
Converting mixed plastics polymers to true recycled plastics
The organocatalyst deconstructs the plastics at different temperatures, which facilitates sequentially recovering the individual monomers separately, in reusable form. Polycarbonates deconstruct at 266° F (130° C), polyurethanes at 320° F (160° C), polyethylene terephthalates at 356° F (180° C) and polyamides at 410° F (210° C). Other plastics, additives and associated materials such as cotton and plastic bags are left intact because of the differences in their reactivity and can subsequently be recovered.
"The deconstructed monomers and the organocatalyst are water soluble, so we can transfer them into water, where any impurities such as pigments can be removed by filtration," said Md Arifuzzaman, the study's lead author and former postdoctoral synthetic organic chemist at ORNL. He is now an Innovation Crossroads Fellow and CEO and Founder of the Re-Du Company.
"The nearly pure monomers are then extracted, leaving the catalyst, which is almost entirely recovered by evaporating the water and can be directly reused for multiple deconstruction cycles."
More information: Md Arifuzzaman et al, Selective deconstruction of mixed plastics by a tailored organocatalyst, Materials Horizons (2023). DOI: 10.1039/D3MH00801K
Journal information: Materials Horizons
Provided by Oak Ridge National Laboratory