This article has been reviewed according to Science X's editorial process and policies. Editors have highlighted the following attributes while ensuring the content's credibility:
fact-checked
proofread
Team designs nitride-reinforced NbMoTaWHfN refractory high-entropy alloy
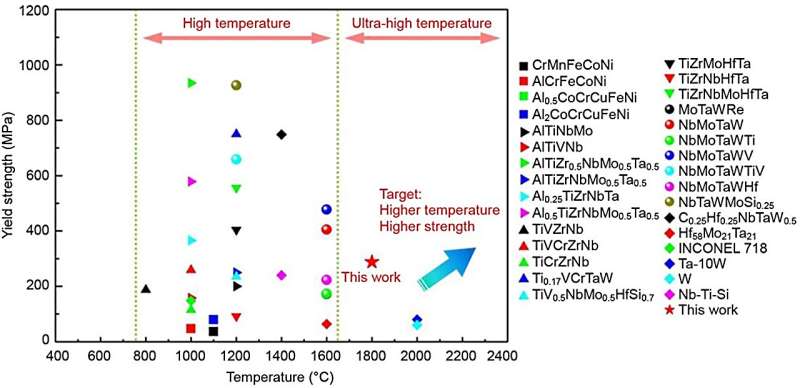
A new generation of refractory alloys with excellent high-temperature performance is urgently demanded for aero-engines, gas turbines, and nuclear power plants. As the service temperature of their hot-ends is reaching 1800 °C or even higher, traditional superalloys can hardly fulfill the temperature demands. Mainly composed of refractory metal elements, refractory high-entropy alloys (RHEAs) exhibit enhanced strength at temperatures above 1,200° C, causing them to attract a great deal of attention.
Some instructive work has been done to develop new alloys with improved ductility and enhanced high-temperature strength for engineering applications by adding other elements based on NbMoTaW and TiZrHfNb RHEAs, such as Ti, Zr, Hf, Re, Si, C, and N. The main strengthening mechanism is solid-solution strengthening, second-phase strengthening, and high softening temperature. If a large number of solute atoms gather around dislocations, they will hinder the movement of dislocations.
When a moving dislocation encounters the second phase, a dislocation ring will form, increasing the required external force, which provides the deformation force. Besides, high-temperature strength is generally related to softening temperature. The softening temperature for an alloy is approximately 0.6Tm (where the melting temperature, Tm, is given in K). Unfortunately, little has been reported about alloys showing promising engineering application strengths at 1,800° C or above thus far.
Considering the high-temperature strength of the NbMoTaWHf RHEA and the excellent thermal stability of nitrides, the secondary strengthening of nitrides on a NbMoTaWHf-base alloy seems to be an efficient approach to realize the "win–win" situation of high temperature and high strength at ultra-high temperatures.
A research team at the Defense Innovation Institute of China led by Professor Xiubing Liang has designed a nitride-reinforced NbMoTaWHfN refractory high-entropy alloy, which shows extremely high compressive yield strengths at temperatures between 1,000 and 1,800° C. The findings are published in Engineering.
This team studied the microstructures and mechanical properties of the NbMoTaW(HfN)x (x = 0, 0.3, 0.7, and 1) RHEAs first. The alloys consist of multiple phases of body-centered cubic (BCC), hafnium nitride (HfN), or multicomponent nitride (MN) phases. As the x contents increase, the grain size becomes smaller, and the strength gradually increases.
Then, the team studied the phase constitution and high-temperature properties of the NbMoTaWHfN RHEA, as it possesses typical microstructures and better mechanical properties. The compressive yield strengths of the NbMoTaWHfN RHEA at ambient temperature, 1,000° C, 1,400° C, and 1,800° C were found to be 1,682 MPa, 1,192 MPa, 792 MPa, and 288 MPa, respectively. The high-temperature strength of this alloy is an inspiring result that exceeds the high temperature and strength of most known alloys, including high-entropy alloys, refractory metals, and superalloys.
Within the paper, the researchers discuss the phase formation mechanism of the HfN and MN phases from the aspect of enthalpies of mixing. Then the strengthening mechanism of NbMoTaW(HfN)x at ambient and elevated temperatures is discussed. The HfN phase has a significant effect on the alloy's high-temperature strength due to its high structural stability and sluggish grain coarsening.
Finally, the research discusses the superior mechanical properties of the NbMoTaWHfN RHEA compared with various alloys. Its superior properties endow the NbMoTaWHfN RHEA with potential for wide-ranging engineering applications at ultra-high temperatures, such as aero-engine and ground gas turbine.
More information: Yixing Wan et al, A Nitride-Reinforced NbMoTaWHfN Refractory High-Entropy Alloy with Potential Ultra-High-Temperature Engineering Applications, Engineering (2023). DOI: 10.1016/j.eng.2023.06.008
Provided by Engineering