This article has been reviewed according to Science X's editorial process and policies. Editors have highlighted the following attributes while ensuring the content's credibility:
fact-checked
peer-reviewed publication
trusted source
proofread
Stick-to-itiveness: Engineers show self-organization of sticky micron-to-mesoscale 3D structures in confined fluids
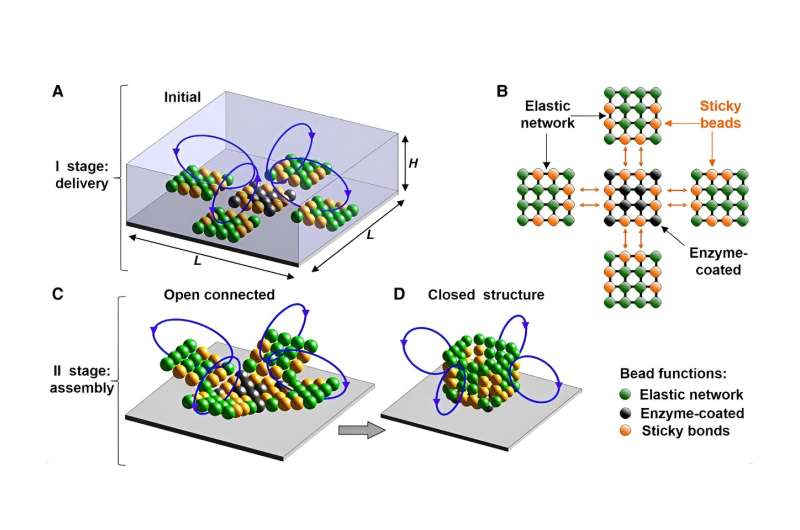
Automating the construction of three-dimensional structures that are 10s of millimeters in size would revolutionize manufacturing of devices for optical, electrical and biomedical applications. An economical process for constructing such 3D microstructures would be to "program" the constituent parts to spontaneously come together and build the structures themselves. Driving micron to mesoscale components (roughly between 0.1 to 100 millimeters) to line up and dynamically assemble into the desired structures, however, remains an elusive goal.
Chemical engineering researchers at the University of Pittsburgh Swanson School of Engineering have built upon their previous research to overcome the challenge of designing such properly self-aligning structures by using fluid mechanics, chemo-mechanical processes—and a little stickiness.
Their research, "Engineering confined fluids to autonomously assemble hierarchical 3D structures," was published in PNAS Nexus. Lead author is Oleg E. Shklyaev, post-doctoral associate with Anna Balazs, Distinguished Professor of Chemical and Petroleum Engineering and the John A. Swanson Chair of Engineering, with former post-doc Abhrajit Laskar.
"One of the fundamental challenges in building anything with micron sized building blocks is to get the blocks to robustly organize on their own, with little intervention from external tools, which could interfere with the dynamic self-assembly," Balazs explained. "What's wonderfully brilliant about the system that Oleg designed is that the naturally occurring interplay between the fluid and chemistry performs the work to spontaneously construct a robust system."
Via computer modeling, Shklyaev designed two-dimensional polymeric sheets with one heavier sheet forming the foundation or base, and the other lighter sheets as the construction panels. Sticky bonds are added to specific points on the sheets to act as hinges—similar to DNA molecule bonds (A,C, G, T) which are designed to precisely fit together.
The panels are then dropped into a solution and sink to the bottom in random areas of the tank. The addition of a reactant to the solution instigates a catalytic reaction, which generates fluid flows that have velocities both vertical and horizontal to the confining walls. The horizontal flow first moves the sheets together along the chamber floor, and the sticky bonds connect the appropriate panel to the base.
Next, the vertical flow lifts the sides of the structure into the upright position, where again the panels are connected via sticky bonds to complete the structure.
"This conversion of chemical energy (released from the catalytic reaction) into mechanical action (fluid flow) is an inherent property of the system. Namely, as the catalytic reaction converts reactants into products, it intrinsically produces density or concentration gradients in the solution. The gradients, in turn, generate a force that acts on the fluid and triggers the flow. The flow acts like 'helping hands' to assemble the structure," Shklyaev explained.
"Through chemistry, you can engineer the spatially and temporally varying patterns that emerge in the flow, and thereby tailor the work done by these hands, which also initiate the cascade of events that leads to building a regular tetrahedron, cube, or similar structure. In principle, the 'sticky' bonds on the panels can involve strands of DNA; the complementarity of DNA strands enables the bonds to be highly selective and recognize the regions to which it should stick."
Closing the lid on the experiment
By engineering the fluid flows, Shklyaev could drive the self-organization of a cube and the closing of the cube's lid, so that the entire structure resembled a takeout box. The chemically generated fluid flow acting on the panels (through mechanisms knows as solutal buoyancy and diffusioosmosis) eventually reaches a dynamic steady state as it completes the assembly of the object, which could later be removed out of the fluid and maintain its integrity.
To further illustrate the potential of the fluidic machinery, the tops of each panel were decorated with long whiskers. As the panels fold upward and the whiskers extend into the fluid flow, the resulting forces drive the whiskers to rotate, much like moving propellers. Sticky bonds could be added to the whiskers to attract bacteria or other materials that need to be removed from the system.
"The use of chemical reactions to tailor the flow to act as a mechanical tool has not been broadly applied in man-made systems, but is particularly valuable since the fluid flow performs the necessary work and replaces complicated machinery," Balazs said. "The process is scalable; multiple structures with different shapes can be formed at one time."
"By providing these guidelines to experimentalists, we can automate manufacturing processes since the structure formation is driven by the dynamic self-assembly of the components. The resulting structures can be used for medical applications since the processes typically involve water, which provides a biologically friendly environment."
More information: Oleg E Shklyaev et al, Engineering confined fluids to autonomously assemble hierarchical 3D structures, PNAS Nexus (2023). DOI: 10.1093/pnasnexus/pgad232
Journal information: PNAS Nexus
Provided by University of Pittsburgh